
10 Types of Ancillary Equipment for Industrial Robotic Systems
Trent Wideman | 3 September 2020
Now, more than ever, companies struggle to staff industrial areas due to the ongoing labor shortage. Pair this with slim margins, and the need to improve efficiencies, lower labor costs, and improve quality is magnified. One avenue to accomplish this, is through an industrial robotic system. Robotic systems can accomplish many tasks within an industrial environment, including palletizing, depalletizing, case packing, machine tending, and many other roles.
While the robotic arm is the focal point of a robotic system, the robot is only as good as it’s ancillary equipment within the system. Here are some of the most commonly integrated ancillary equipment that can help increase the scope handled by a robotic system.
Pallet dispensers automate the singulation and dispensing of empty pallets. At Bastian Solutions, we utilize both a fork style and a lift style pallet dispenser, depending on type and overall quality of the pallet. These dispensers can typically hold up to 20 pallets at a time, which allow for operators to complete other value-added tasks while pallets are automatically dispensed and conveyed to have product placed onto them.
Opposite to pallet dispensers, there are pallet stackers, which complete the same task as dispensers, but in complete opposition. Pallet dispensers are commonly used within robotic depalletizing systems in which inbound pallet loads are completely depleted of their contents. The pallets are then stacked and queued for pickup by an operator.
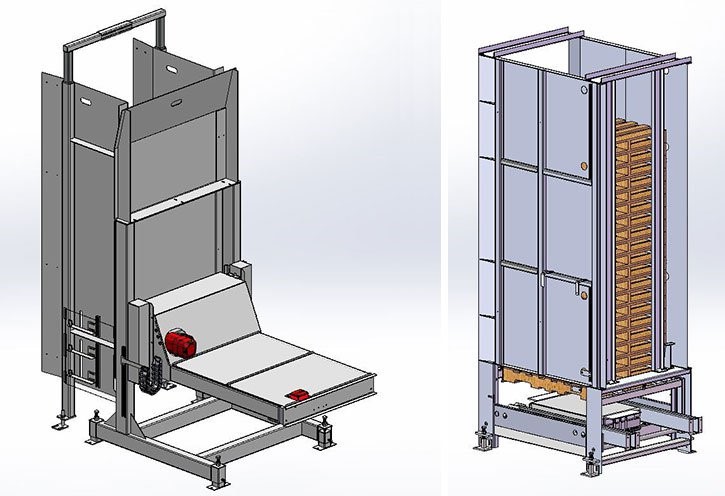
Pallet Conveyor
Pallet conveyor allows for automatic transport and presentation of pallets within the robotic system. Bastian Solutions manufactures both Chain Driven Live Roller or CDLR pallet conveyor and Drag Chain pallet conveyor. Both CDLR and drag chain conveyor have their specific applications for use. CDLR is available in various roller center dimensions depending on the pallet type, the load weight, and the stability of the load. Drag Chain is available in 2 strand, 3 strand, or even up to 5 strand configurations, depending on the load specifications. Additional zones of pallet conveyor can also be utilized to increase accumulation of pallet loads, thus allowing for a decrease in the frequency a fork truck operator will need to tend to the system to pick or place a pallet load.
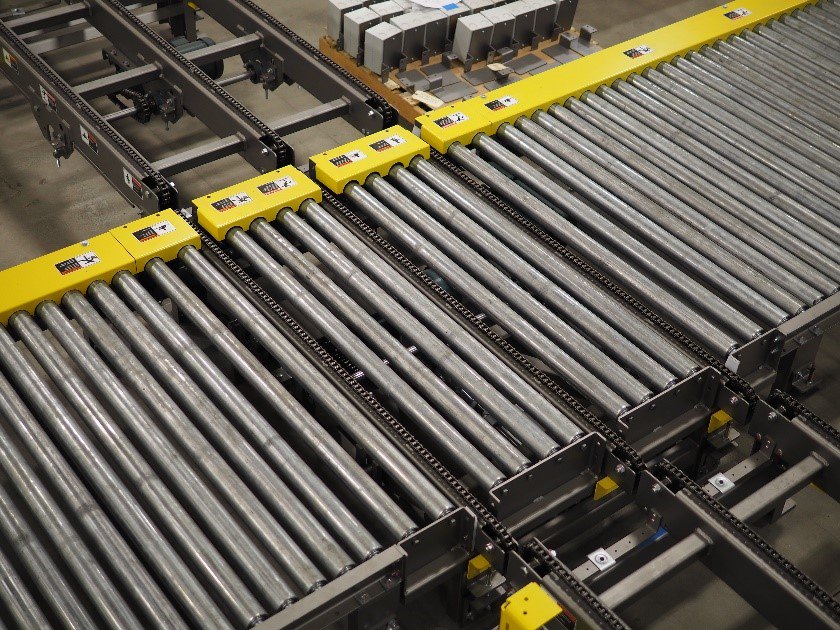
Another avenue that can be utilized to transport full or empty pallets throughout the system, is a shuttle car. Shuttle cars utilize a floor mounted linear track and a shuttle with a conveyorized top to transport pallets. Often, shuttle cars are an ideal alternative over pallet conveyor trunk lines with multiple pop-up transfers.
If space near a robotic system is limited, an Autonomous Guided Vehicle or AGV can also be a viable alternative to transport pallets. Unlike pallet conveyor or shuttle cars, AGVs do not require any physical equipment that may impede on neighboring systems or aisle ways. AGVs can transport both empty pallets and complete loads to and from the robotic system. They also are not limited in range, as AGVs can be programmed to transport pallets to any location within a facility.
Infeed Conveyor
Regardless of the application, there is likely a need for a conveyor to transport the product to or from the robot. In case of a robotic palletizing application, the infeed conveyor transports the product into the robot’s reach envelope to facilitate the pick and placement of the product. Often, the infeed conveyor also justifies the product to a known location to allow for the robot to have a repeatable location to pick from. Means to justify product coming in includes a pneumatic pusher, skewed rollers, or a blade stop to orient cases to a desired position. Conveyor has many hats and can accommodate a range of products from corrugate RSC cases all the way to large off roading tires.
Robot Stands
Robot stands are an essential part of a robotic system. Stands are utilized to optimize the robot reach within the cell. A robotic arm’s reach envelope is similar shape to an inner tube, so it is vital that all necessary equipment is within the reach of the robot. For each robotic system project, a reach study is completed that evaluates all aspects of the system that the robot interacts with to help determine the optimal height for the stand.
Vision Systems
Vision systems provide a means to locate parts within a robotic system that may not be in a repeatable location. Vision systems within a robotic cell can be provided either through the robot manufacturer or through a 3rd party vision vendor. These systems come in wide array of configurations ranging from 2D to 3D vision or having the vision system mounted to the robot or having it fixed mounted on a stand. A common application for a vision system is to locate cases or parts on a pallet within a robotic depalletizing system.
Bottom & Top Sheet Dispensers
Within robotic palletizing applications, a common requirement is the need for slip sheets or top sheets within the pallet load. These sheets can be applied utilizing an ancillary sheet dispenser. Bastian Solutions utilizes a gantry style sheet dispenser. The gantry picks a single sheet from a bulk stack within a bin. The sheet is then transported and placed on top of the pallet or pallet load. The bin can be configured to be outside of the safety fencing of the cell so that stacks of sheets can be replenished without stopping the system.
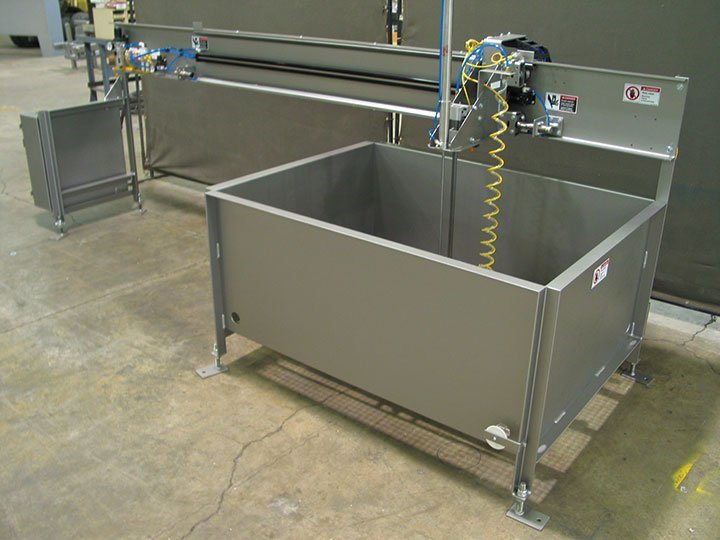
Sheet Bins
Sheet bins are commonly used in lieu of a sheet dispenser, if the rate of product handled allows. If the robot is not heavily utilized to keep up with the rate, the robot can be used to pick and place the sheets from a bin. This is done by placing the sheet bin within the robot’s reach envelope and utilizing vacuum cups on the end of arm tooling to pick the sheet.
Stretch Wrappers
Stretch wrappers provide a means to automatically apply stretch wrap to an outbound pallet load. Wrappers can come in various configurations such as turntable style or rotary arm style, dependent on load size and the rate at which outbound pallets are produced. While many facilities have in-place semi-automatic stretch wrappers within their facility, it is often worth the time to assess if an in-line stretch wrapper is beneficial to your robotic system. Having a stretch wrapper local to the robotic system allows for the elimination of double handling by your fork truck operators as well as increased system autonomy, as the wrapper will be integrated with the robotic system, eliminating the need for an operator to begin the wrapping cycle. Many stretch wrapper vendors also offer additional equipment such as strapping machines that are utilized to apply either a vertical or horizontal strap to increase the stability of the load.
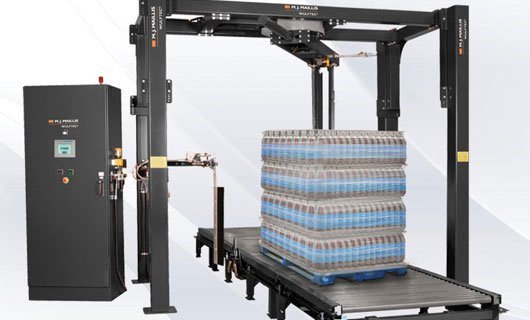
Labelers
Pallet labelers allow for the automatic application of labels within the robotic system. This can include a case labeler to apply a label to each individual case or a pallet labeler for the entire outbound load. Like stretch wrappers, labelers come in multiple configurations and can be designed to apply labels to multiple sides of cases or pallet loads. Pallet labels can also be populated with various information ranging from simple time and date information to custom barcodes that are communicated from the facility WMS system.
In summary, the question is likely not if ancillary equipment brings value to your robotic system, but rather what ancillary equipment makes sense for your system. By adding additional equipment, the ideal system can be configured to automate your process.
Have an idea of how a robotic system could meet your automation plans? Contact our team and discuss how we, at Bastian Solutions, can help you meet your long-term goals!
Trent is a field application engineer with the robotics group of Bastian Solutions in St. Louis, MO. He has a Bachelor of Science degree in Industrial & Manufacturing Systems Engineering from the University of Missouri – Columbia. As a field application engineer, his duties include working with clients to determine their material handling needs and developing layouts for robotic systems.
Comments
No comments have been posted to this Blog Post
Leave a Reply
Your email address will not be published.
Comment
Thank you for your comment.